Destylator przemysłowy to urządzenie, które odgrywa kluczową rolę w procesach separacji cieczy na podstawie różnic w ich temperaturach wrzenia. W praktyce, destylacja polega na podgrzewaniu mieszaniny cieczy, co prowadzi do odparowania substancji o niższej temperaturze wrzenia. Para ta następnie jest schładzana i kondensowana z powrotem do stanu ciekłego, co pozwala na oddzielenie jej od pozostałych składników. W przemyśle chemicznym i petrochemicznym, destylatory są wykorzystywane do oczyszczania surowców oraz produkcji różnych substancji chemicznych. W zależności od zastosowania, destylatory mogą mieć różne konstrukcje, takie jak kolumnowe czy prostokątne. Warto również zauważyć, że proces destylacji może być przeprowadzany w różnych warunkach ciśnienia, co wpływa na efektywność separacji.
Jakie są różnice między destylatorem a innymi urządzeniami
W kontekście przemysłowym istnieje wiele metod separacji cieczy, jednak destylator wyróżnia się na tle innych urządzeń ze względu na swoją specyfikę działania. Na przykład, w przeciwieństwie do filtrów czy wirówek, które opierają się głównie na różnicach gęstości lub wielkości cząsteczek, destylacja bazuje na różnicach temperatur wrzenia substancji. Dzięki temu możliwe jest skuteczne oddzielanie cieczy o podobnych właściwościach fizycznych. Kolejną istotną różnicą jest to, że destylatory mogą być używane do przetwarzania dużych ilości materiału w sposób ciągły, co czyni je bardziej efektywnymi w porównaniu do batchowych metod separacji. Dodatkowo, destylatory mogą być dostosowane do specyficznych potrzeb produkcyjnych poprzez modyfikacje konstrukcyjne oraz zastosowanie różnych technologii chłodzenia i podgrzewania.
Jakie są zastosowania destylatorów przemysłowych w różnych branżach
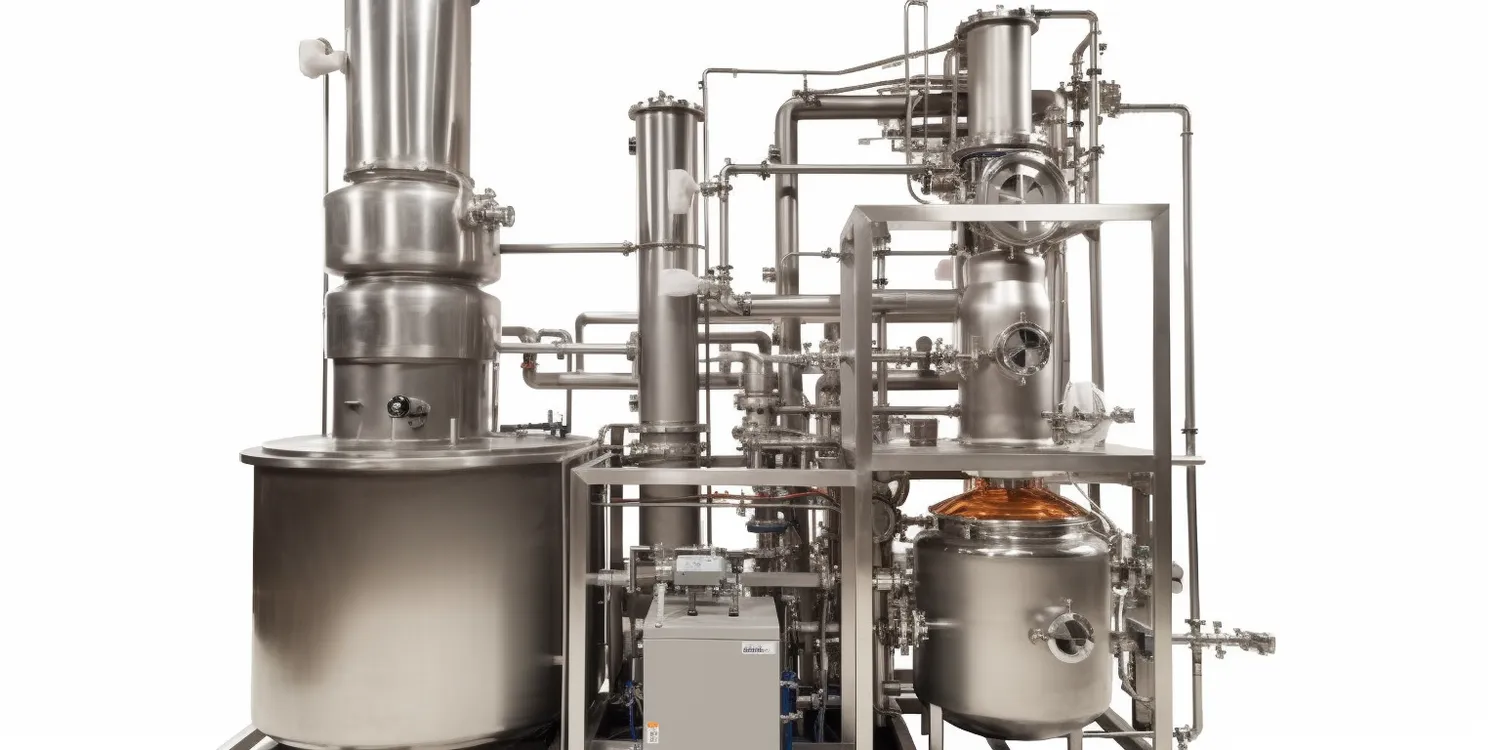
Destylatory przemysłowe znajdują szerokie zastosowanie w wielu branżach, co czyni je niezbędnym elementem nowoczesnej produkcji. W przemyśle chemicznym są wykorzystywane do oczyszczania surowców oraz produkcji substancji chemicznych takich jak alkohole czy kwasy organiczne. W branży petrochemicznej destylacja jest kluczowym procesem w rafinacji ropy naftowej, gdzie pozwala na uzyskanie różnych frakcji paliwowych oraz olejów. Ponadto, w przemyśle spożywczym destylatory służą do produkcji napojów alkoholowych takich jak whisky czy gin, gdzie proces ten ma kluczowe znaczenie dla uzyskania odpowiednich walorów smakowych i aromatycznych. Również w farmaceutyce destylacja jest stosowana do oczyszczania substancji czynnych oraz rozpuszczalników.
Jakie są najnowsze technologie stosowane w destylatorach
W ostatnich latach technologia destylacji uległa znacznemu rozwojowi dzięki innowacjom inżynieryjnym oraz postępom w dziedzinie automatyzacji i monitorowania procesów. Nowoczesne destylatory często wykorzystują zaawansowane systemy sterowania, które umożliwiają precyzyjne zarządzanie parametrami procesu, takimi jak temperatura czy ciśnienie. Dzięki temu możliwe jest zwiększenie efektywności energetycznej oraz poprawa jakości uzyskiwanych produktów. Dodatkowo, pojawiły się nowe materiały konstrukcyjne, które zwiększają odporność urządzeń na korozję i wysokie temperatury, co wydłuża ich żywotność i zmniejsza koszty eksploatacyjne. Innowacje obejmują również zastosowanie technologii membranowej oraz ekstrakcji cieczy nadkrytycznej jako alternatywnych metod separacji.
Jakie są kluczowe elementy konstrukcyjne destylatora przemysłowego
Konstrukcja destylatora przemysłowego jest złożona i składa się z wielu kluczowych elementów, które współpracują ze sobą w celu efektywnego przeprowadzenia procesu destylacji. Podstawowym elementem jest zbiornik, w którym odbywa się podgrzewanie cieczy. Zbiornik ten musi być wykonany z materiałów odpornych na wysokie temperatury oraz korozję, aby zapewnić długotrwałe użytkowanie. Kolejnym istotnym komponentem jest kolumna destylacyjna, która jest odpowiedzialna za separację pary od cieczy. W kolumnie znajdują się różne elementy, takie jak wypełnienia czy talerze, które zwiększają powierzchnię kontaktu między parą a cieczą, co sprzyja efektywnemu oddzielaniu składników. Po kondensacji pary, ciecz trafia do odbiornika, gdzie jest zbierana i może być dalej przetwarzana lub pakowana. Dodatkowo, destylatory często wyposażone są w systemy chłodzenia, które pozwalają na efektywne skraplanie pary oraz odzyskiwanie energii.
Jakie są wyzwania związane z eksploatacją destylatorów przemysłowych
Eksploatacja destylatorów przemysłowych wiąże się z różnymi wyzwaniami, które mogą wpływać na wydajność i jakość produkcji. Jednym z głównych problemów jest konieczność ciągłego monitorowania parametrów procesu, takich jak temperatura czy ciśnienie. Niewłaściwe ustawienia mogą prowadzić do nieefektywnej separacji lub nawet uszkodzenia urządzenia. Ponadto, regularne czyszczenie i konserwacja są niezbędne, aby zapobiec osadzaniu się zanieczyszczeń na ściankach kolumny czy w innych częściach destylatora. Zanieczyszczenia te mogą znacząco obniżyć efektywność procesu oraz jakość uzyskiwanych produktów. Innym wyzwaniem jest zarządzanie zużyciem energii, ponieważ proces destylacji może być energochłonny. W związku z tym wiele zakładów stara się wdrażać technologie zwiększające efektywność energetyczną oraz korzystać z odnawialnych źródeł energii.
Jakie są korzyści płynące z automatyzacji procesów w destylacji
Automatyzacja procesów w destylacji przynosi wiele korzyści zarówno dla producentów, jak i dla jakości uzyskiwanych produktów. Dzięki zastosowaniu nowoczesnych systemów sterowania możliwe jest precyzyjne monitorowanie i regulowanie parametrów procesu w czasie rzeczywistym. To z kolei pozwala na szybsze reagowanie na ewentualne problemy oraz minimalizację ryzyka wystąpienia błędów ludzkich. Automatyzacja przyczynia się również do zwiększenia wydajności produkcji poprzez optymalizację cykli pracy urządzeń oraz zmniejszenie czasu przestoju. Dodatkowo, dzięki zastosowaniu technologii analitycznych można lepiej kontrolować jakość produktów końcowych, co ma kluczowe znaczenie w branżach wymagających wysokich standardów jakościowych, takich jak farmaceutyka czy przemysł spożywczy. Wprowadzenie automatyzacji pozwala także na redukcję kosztów operacyjnych poprzez zmniejszenie zużycia energii oraz materiałów eksploatacyjnych.
Jakie są różnice między destylacją prostą a frakcyjną
Destylacja prosta i frakcyjna to dwa podstawowe typy procesów destylacyjnych, które różnią się od siebie zarówno pod względem zastosowania, jak i mechanizmu działania. Destylacja prosta polega na jednorazowym podgrzewaniu mieszaniny cieczy i skraplaniu pary bez dodatkowych etapów separacji. Jest to metoda stosunkowo prosta i najczęściej wykorzystywana do oddzielania substancji o znacznie różniących się temperaturach wrzenia. Przykładem może być oczyszczanie alkoholu etylowego z wodą. Z kolei destylacja frakcyjna to bardziej zaawansowany proces, który umożliwia separację składników o podobnych temperaturach wrzenia poprzez wielokrotne skraplanie i odparowywanie pary w kolumnie frakcyjnej. Dzięki temu możliwe jest uzyskanie wyższej czystości produktów oraz dokładniejsze oddzielanie poszczególnych składników mieszaniny.
Jakie są kluczowe czynniki wpływające na efektywność destylacji
Efektywność procesu destylacji zależy od wielu czynników, które mają wpływ na jakość i ilość uzyskiwanych produktów. Jednym z najważniejszych czynników jest temperatura podgrzewania cieczy oraz ciśnienie panujące w układzie. Odpowiednie ustawienie tych parametrów pozwala na optymalne oddzielenie składników mieszaniny. Kolejnym istotnym czynnikiem jest konstrukcja kolumny destylacyjnej oraz zastosowane materiały wypełniające lub talerze, które zwiększają powierzchnię kontaktu między parą a cieczą. Im większa powierzchnia kontaktu, tym lepsza separacja składników o podobnych temperaturach wrzenia. Również czas trwania procesu ma znaczenie; zbyt krótki czas może prowadzić do niedostatecznej separacji, podczas gdy zbyt długi może skutkować stratami cennych substancji.
Jakie są przyszłościowe kierunki rozwoju technologii destylacyjnej
Przemysłowa technologia destylacyjna stale ewoluuje w odpowiedzi na rosnące wymagania dotyczące efektywności energetycznej oraz jakości produktów końcowych. W przyszłości możemy spodziewać się dalszego rozwoju technologii automatyzacji procesów destylacyjnych, co pozwoli na jeszcze lepsze monitorowanie i kontrolę parametrów produkcji. Wprowadzenie sztucznej inteligencji do systemów sterowania może przyczynić się do optymalizacji procesów oraz przewidywania ewentualnych problemów zanim one wystąpią. Kolejnym kierunkiem rozwoju będzie zwiększona integracja procesów chemicznych z technologiami odzysku energii oraz recyklingu materiałów, co wpłynie na bardziej zrównoważony rozwój przemysłu chemicznego i pokrewnych branż. Również badania nad nowymi materiałami konstrukcyjnymi mogą prowadzić do stworzenia bardziej odpornych i efektywnych urządzeń destylacyjnych.
Jakie są kluczowe aspekty bezpieczeństwa w pracy z destylatorami
Bezpieczeństwo w pracy z destylatorami przemysłowymi jest niezwykle istotnym zagadnieniem, które wymaga szczególnej uwagi ze strony operatorów oraz zarządzających zakładami. Przede wszystkim, należy zapewnić odpowiednie szkolenia dla pracowników, aby byli świadomi potencjalnych zagrożeń związanych z obsługą urządzeń. Kluczowe jest również stosowanie odpowiednich środków ochrony osobistej, takich jak odzież ochronna, rękawice czy okulary. Dodatkowo, systemy wentylacyjne powinny być regularnie kontrolowane, aby zapobiec gromadzeniu się niebezpiecznych oparów. Warto również wdrożyć procedury awaryjne na wypadek wystąpienia nieprzewidzianych sytuacji, takich jak wycieki substancji chemicznych czy pożary. Regularne przeglądy techniczne i konserwacja urządzeń są niezbędne do utrzymania ich w dobrym stanie i minimalizacji ryzyka awarii.