Destylarki do rozpuszczalników to urządzenia, które wykorzystują proces destylacji do oddzielania różnych substancji chemicznych na podstawie ich temperatury wrzenia. W praktyce oznacza to, że gdy mieszanina rozpuszczalników jest podgrzewana, substancje o niższej temperaturze wrzenia parują jako pierwsze. Para ta następnie przechodzi przez chłodnicę, gdzie skrapla się i zbiera w osobnym naczyniu. W ten sposób można uzyskać czystszy produkt, eliminując zanieczyszczenia oraz inne składniki, które mogą wpływać na jakość końcowego rozpuszczalnika. W zależności od konstrukcji destylarki, proces ten może być bardziej lub mniej efektywny. Niektóre modele są zaprojektowane do pracy z dużymi ilościami materiału, co czyni je idealnymi dla przemysłu chemicznego, podczas gdy inne są bardziej kompaktowe i przeznaczone do użytku laboratoryjnego.
Jakie są najpopularniejsze rodzaje destylarek do rozpuszczalników
Na rynku dostępnych jest wiele różnych typów destylarek do rozpuszczalników, a ich wybór zależy od specyficznych potrzeb użytkownika. Najpopularniejsze modele to destylarki prostokątne oraz okrągłe, które różnią się kształtem i konstrukcją. Destylarki prostokątne często mają większą pojemność i są bardziej wydajne w przypadku dużych ilości materiału. Z kolei destylarki okrągłe charakteryzują się lepszym przepływem pary, co może prowadzić do wyższej jakości uzyskiwanego produktu. Innym popularnym rodzajem są destylarki rotacyjne, które umożliwiają delikatną destylację w niskich temperaturach, co jest szczególnie ważne w przypadku substancji wrażliwych na ciepło. Istnieją również destylarki próżniowe, które pozwalają na obniżenie ciśnienia wewnętrznego, co z kolei obniża temperaturę wrzenia substancji i umożliwia ich separację bez degradacji.
Jakie zastosowania mają destylarki do rozpuszczalników w przemyśle
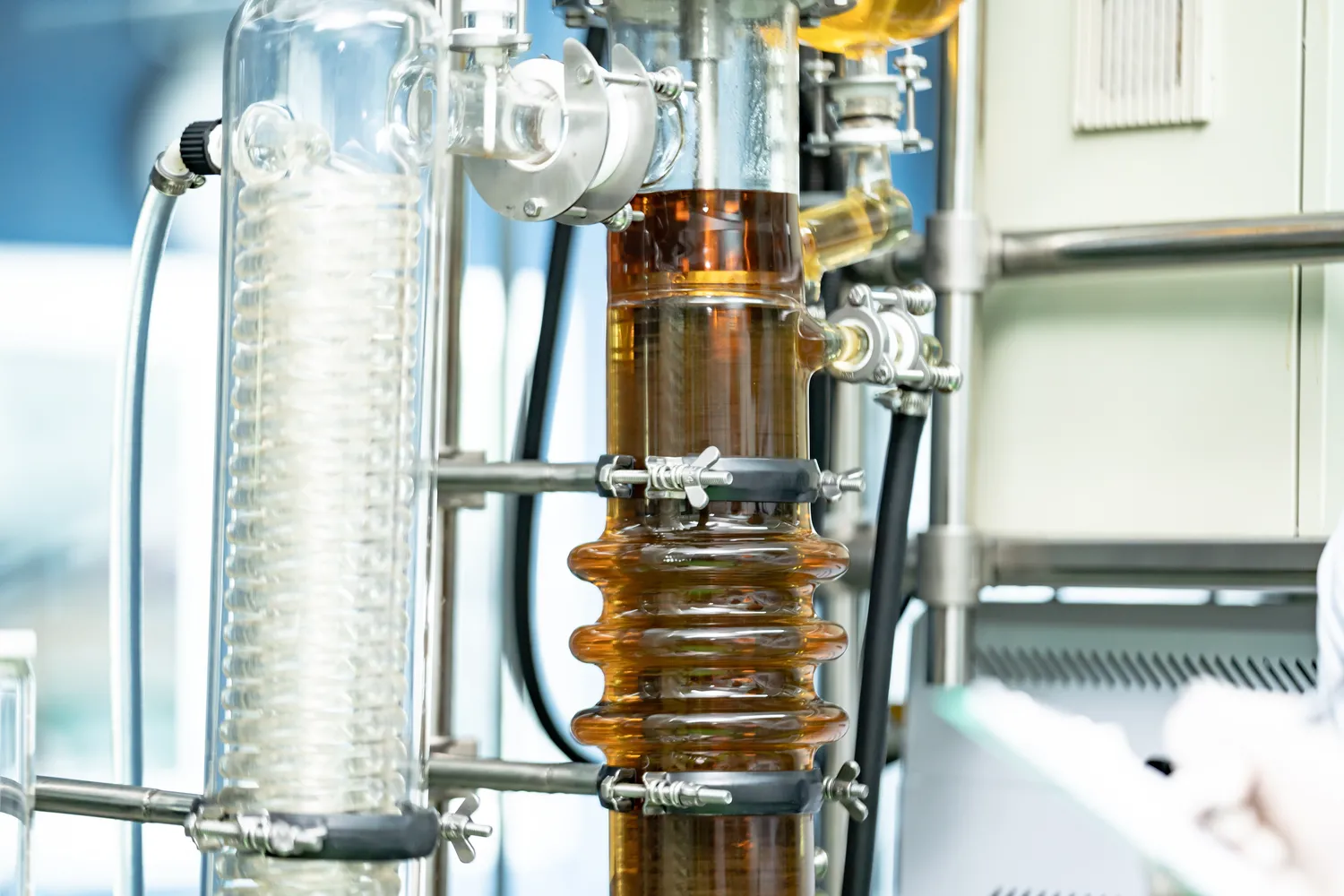
Destylarki do rozpuszczalników znajdują szerokie zastosowanie w różnych gałęziach przemysłu chemicznego oraz farmaceutycznego. W przemyśle chemicznym służą one do oczyszczania surowców oraz produkcji wysokiej jakości rozpuszczalników wykorzystywanych w procesach produkcyjnych. Dzięki możliwości separacji substancji o różnych temperaturach wrzenia można uzyskać czyste produkty, które spełniają rygorystyczne normy jakościowe. W branży farmaceutycznej destylarki są niezbędne do produkcji leków oraz substancji czynnych, gdzie czystość składników ma kluczowe znaczenie dla bezpieczeństwa pacjentów. Oprócz tego destylarki są wykorzystywane w laboratoriach badawczych do analizy chemicznej oraz syntez organicznych. Umożliwiają one naukowcom izolację i oczyszczanie związków chemicznych, co jest niezbędne w procesie badań nad nowymi lekami czy materiałami.
Jakie są kluczowe czynniki przy wyborze destylarki do rozpuszczalników
Wybór odpowiedniej destylarki do rozpuszczalników jest kluczowy dla efektywności procesu destylacji oraz jakości uzyskiwanego produktu. Przy podejmowaniu decyzji warto zwrócić uwagę na kilka istotnych czynników. Pierwszym z nich jest pojemność urządzenia, która powinna być dostosowana do przewidywanych ilości materiału przeznaczonego do destylacji. Kolejnym ważnym aspektem jest rodzaj stosowanych materiałów budowlanych; niektóre substancje chemiczne mogą reagować z metalami lub tworzywami sztucznymi, dlatego warto wybierać urządzenia wykonane z odpornych na korozję materiałów takich jak szkło czy stal nierdzewna. Również wydajność energetyczna destylarki ma znaczenie; nowoczesne modele często oferują lepszą efektywność energetyczną, co przekłada się na niższe koszty eksploatacji. Dodatkowo warto zwrócić uwagę na łatwość obsługi i konserwacji urządzenia; im prostsza konstrukcja i łatwiejszy dostęp do elementów roboczych, tym mniejsze ryzyko awarii oraz większa wygoda użytkowania.
Jakie są najczęstsze problemy z destylarkami do rozpuszczalników
Podczas użytkowania destylarek do rozpuszczalników mogą wystąpić różne problemy, które mogą wpływać na efektywność procesu oraz jakość uzyskiwanego produktu. Jednym z najczęstszych problemów jest zatykanie się rur chłodzących, co może prowadzić do obniżenia wydajności destylacji. Zatykanie to często spowodowane jest osadzaniem się resztek substancji chemicznych, dlatego regularne czyszczenie i konserwacja urządzenia są kluczowe dla jego prawidłowego funkcjonowania. Innym problemem może być niewłaściwe ustawienie temperatury, co skutkuje niepełnym oddzieleniem składników mieszaniny. W takim przypadku konieczne jest dostosowanie parametrów pracy destylarki, aby uzyskać pożądany efekt. Często występującym problemem są także wycieki, które mogą być wynikiem uszkodzeń uszczelek lub nieprawidłowego montażu elementów. Warto regularnie sprawdzać stan techniczny destylarki oraz wymieniać zużyte części, aby uniknąć poważniejszych awarii.
Jakie są zalety korzystania z destylarek do rozpuszczalników
Korzystanie z destylarek do rozpuszczalników niesie ze sobą wiele korzyści, zarówno dla przemysłu, jak i dla użytkowników indywidualnych. Przede wszystkim, proces destylacji pozwala na uzyskanie wysokiej jakości rozpuszczalników, które są wolne od zanieczyszczeń i innych niepożądanych substancji. Dzięki temu można osiągnąć lepsze rezultaty w różnych zastosowaniach chemicznych oraz laboratoryjnych. Kolejną zaletą jest możliwość recyklingu rozpuszczalników; poprzez ich destylację można ponownie wykorzystać substancje chemiczne, co przyczynia się do zmniejszenia kosztów produkcji oraz ograniczenia negatywnego wpływu na środowisko. Destylarki umożliwiają także precyzyjne kontrolowanie procesu separacji składników, co pozwala na dostosowanie parametrów pracy do specyficznych potrzeb użytkownika. Dodatkowo nowoczesne modele destylarek często wyposażone są w zaawansowane systemy monitorowania i automatyzacji, co zwiększa wygodę obsługi oraz bezpieczeństwo pracy.
Jakie są różnice między destylacją prostą a frakcyjną
Destylacja prosta i frakcyjna to dwa podstawowe rodzaje procesów destylacyjnych, które różnią się pod względem zastosowania oraz efektywności separacji składników. Destylacja prosta jest stosunkowo prostym procesem, który polega na podgrzewaniu mieszaniny cieczy i zbieraniu pary o niższej temperaturze wrzenia. Jest to metoda skuteczna w przypadku rozdzielania substancji o znacznie różniących się temperaturach wrzenia. Jednakże w sytuacji, gdy składniki mają zbliżone temperatury wrzenia, efektywność destylacji prostej znacząco maleje. W takich przypadkach lepszym rozwiązaniem jest destylacja frakcyjna, która wykorzystuje kolumny frakcyjne do bardziej precyzyjnego oddzielania składników. Kolumna frakcyjna działa na zasadzie wielokrotnego skraplania i parowania cieczy, co pozwala na uzyskanie wyższej czystości produktów końcowych. Destylacja frakcyjna jest szczególnie przydatna w przemyśle petrochemicznym oraz chemicznym, gdzie konieczne jest oddzielanie wielu różnych składników o podobnych właściwościach fizycznych.
Jakie są najlepsze praktyki przy używaniu destylarek do rozpuszczalników
Aby maksymalizować efektywność działania destylarek do rozpuszczalników oraz zapewnić bezpieczeństwo użytkowania, warto przestrzegać kilku najlepszych praktyk. Przede wszystkim przed rozpoczęciem pracy należy dokładnie zapoznać się z instrukcją obsługi dostarczoną przez producenta. Znajomość zasad działania urządzenia oraz jego specyfikacji technicznych pozwoli uniknąć wielu problemów podczas eksploatacji. Ważne jest również regularne czyszczenie i konserwacja destylarki; osady chemiczne mogą wpływać na wydajność procesu oraz jakość uzyskiwanego produktu. Należy także dbać o odpowiednie warunki pracy; temperatura otoczenia oraz wentylacja pomieszczenia mają kluczowe znaczenie dla bezpieczeństwa użytkowników oraz efektywności działania urządzenia. Podczas pracy z substancjami chemicznymi warto stosować odpowiednie środki ochrony osobistej, takie jak rękawice czy okulary ochronne, aby minimalizować ryzyko kontaktu z niebezpiecznymi substancjami.
Jakie innowacje technologiczne wpływają na rozwój destylarek do rozpuszczalników
W ostatnich latach rynek destylarek do rozpuszczalników przeszedł wiele zmian dzięki innowacjom technologicznym, które znacząco poprawiły ich wydajność oraz funkcjonalność. Nowoczesne modele często wyposażone są w zaawansowane systemy automatyzacji i monitorowania procesów, co pozwala na precyzyjne kontrolowanie parametrów pracy urządzenia bez potrzeby stałej interwencji ze strony operatora. Dzięki temu możliwe jest osiągnięcie większej efektywności energetycznej oraz poprawa jakości uzyskiwanych produktów końcowych. Innowacje obejmują również zastosowanie materiałów kompozytowych i nanotechnologii w budowie elementów roboczych destylarek; takie rozwiązania zwiększają odporność na korozję oraz wydłużają żywotność urządzeń. Również rozwój technologii chłodniczych przyczynia się do poprawy efektywności skraplania pary; nowoczesne systemy chłodzenia charakteryzują się lepszymi parametrami termodynamicznymi, co przekłada się na szybsze i bardziej efektywne procesy separacyjne.
Jakie są koszty zakupu i eksploatacji destylarek do rozpuszczalników
Koszt zakupu i eksploatacji destylarek do rozpuszczalników może znacznie różnić się w zależności od modelu, producenta oraz specyfiki zastosowań. Na rynku dostępne są zarówno tańsze modele przeznaczone do użytku domowego lub laboratoryjnego, jak i drogie przemysłowe urządzenia o dużej wydajności i zaawansowanej technologii. Przy zakupie warto uwzględnić nie tylko cenę samego urządzenia, ale także koszty związane z jego eksploatacją; obejmują one m.in. zużycie energii elektrycznej, konserwację oraz ewentualne naprawy czy wymianę części zamiennych. Koszty eksploatacyjne mogą być znacznie obniżone dzięki wyborowi energooszczędnych modeli lub tych wyposażonych w systemy automatyzacji, które minimalizują czas pracy operatora i zwiększają efektywność procesów.